G1 EBOXX
Manufacturing
For 25 years, Nicolai GmbH has made its business to manufacture high-quality bikes at its own location in Germany. In 1996, we were dissatisfied with the quality of a contract manufacturer and we said to ourselves: “We have to do better!” The CNC machining of complex aluminium components made from 7000 series aluminium in our own factory enables us to create the best products. Similar to aircraft construction, we start with aluminium blocks which are then milled from all directions to create very strong, durable, but also visually appealing components. All components are digitally designed in a CAD system, topologically optimized and FEM calculated. These methods help us to develop lighter and stiffer structures. In the last 25 years a lot has happened in the field of digitization, but the most important tool of a bike engineer remains the experience with different bikes on the trail. In recent years we have often been asked why we do not offer carbon frames. The answer to this question can be found in the company philosophy – we want to produce high quality, robust, durable and recyclable bikes. Bikes that can withstand a fall without worry and without hidden damage in any laminate layers. For 25 years we have been building these bikes from the best aluminium: the 7000 alloy. At NICOLAI, we have been dealing with the subject of electric bikes for over 10-years. With our own products or with engineering services in the field of electromobility, we have built up a second foothold. In the following we will take you on a tour through our company and show you how our new G1-EBOXX bike was created.
DEVELOPMENT / CAD
At NICOLAI, the development of new products is not owned by yearly planned product cycle or ‘show deadlines’, nor does it take place statically at a designer’s desk. Most new products are the result of feedback from test riders, customers, and technical innovations in our manufacturing processes. In the case of the G1-EBOXX, it was the new products from BOSCH that triggered a fresh design of the bike. Smaller, lighter, stronger and quieter are the four facts that summarize the new BOSCH motor. With a weight of 2.9 kg the motor is one of the lightest, combined with 75 Nm torque it is also one of the most powerful.
For the layman, it may sound trivial at first to reconstruct an existing bike around a new motor. Of course, the new motor compatibility could have been achieved simply by changing the motor mount and milling out the battery holder in the down tube. But, for a great E-MTB, precise system integration of the motor and battery is the primary goal. Integrating the components not only includes the installation space but also the protection of the components against environmental and riding influences as well as noise and heat management.
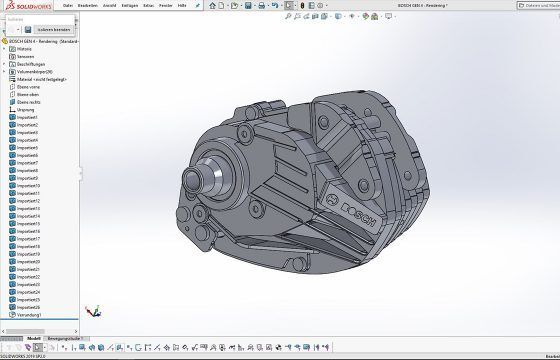
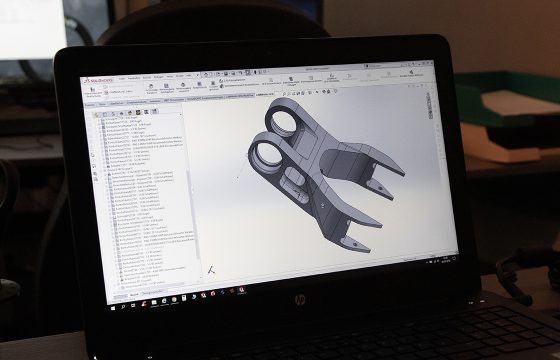
The aim is to create a state-of-the-art E-MTB with our outstanding GEOLUTION geometry, a solid chassis and the unique GATES drive. After the specifications for the new G1-EBOXX Bike had been written and the concept created, the work of Kalle Nicolai, Philipp Hildebrand, and Jens Miller, on the computer with the SOLIDWORKS CAD system began. The construction starts with the calculation of the geometry and the kinematics of the bike. Further steps are the construction of the components by FEM topology optimization, the examination of manufacturability, the compatibility of the components and the assembly ability of the complete bike.
The horseshoe shaped yoke of the swingarm is programmed by Markus Schmidt using CAD and CAM systems. The CAM system allows the CNC machine to be digitally mapped and the milling process to be simulated in advance. The CAM system shows the raw material in light blue and the component to be produced in grey.The finished component after programming the milling paths in the CAM system. The program is then loaded onto the milling machine and the component is produced.
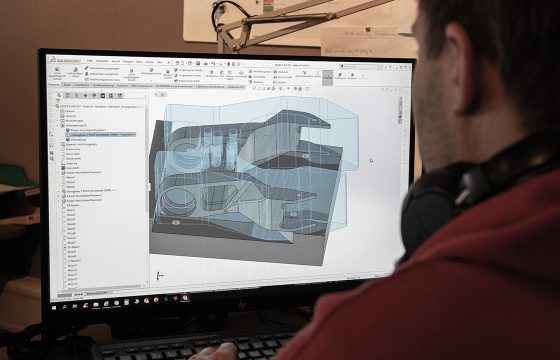
MATERIAL
Machining methods start with the material supplies for production. For the various components, rectangular or round extruded profiles and material blanks made of the most varied 7000 aluminium alloys are available. Special profiles are also produced for some components in order to reduce the volume of waste created as a byproduct.
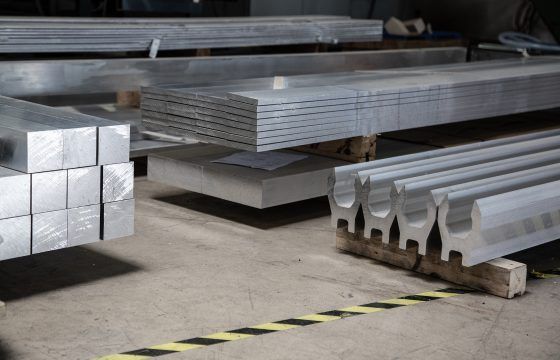
We at NICOLAI use the alloy 7020-T6 (AlZn4.5Mg1) for our frames. Compared to the competitors who mostly use aluminium 6061-T6, this grade has much better strength values. The tensile strength of 7020 compared to 6061 aluminium is about a third higher. The elastic limit is about one fifth higher.
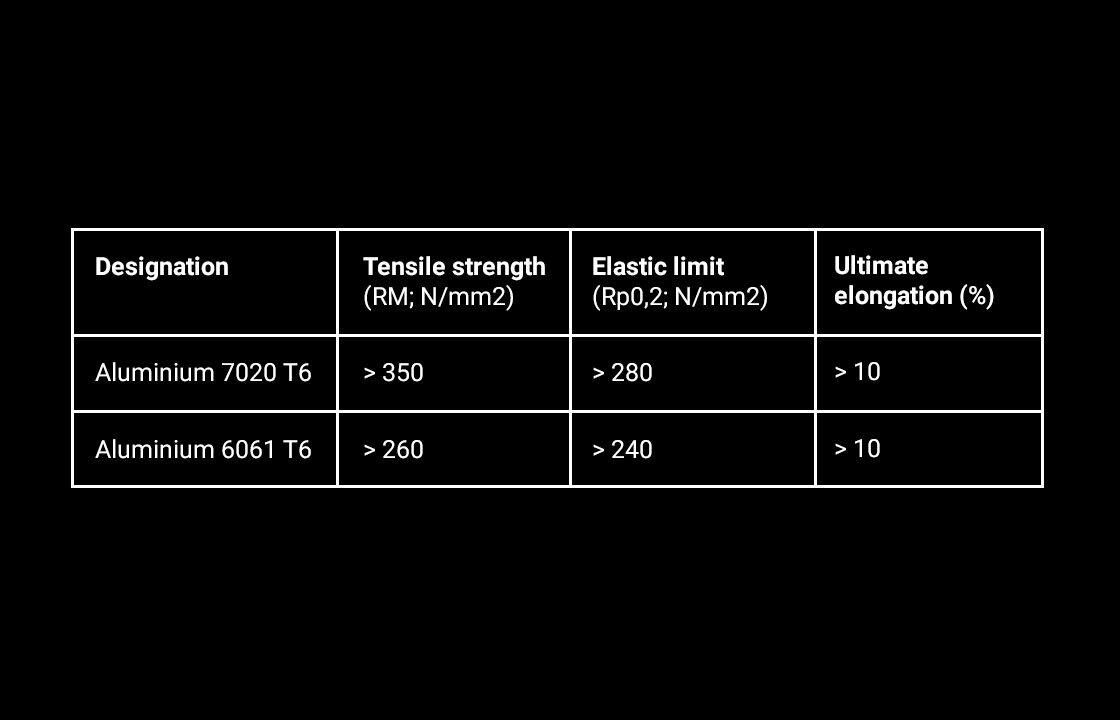
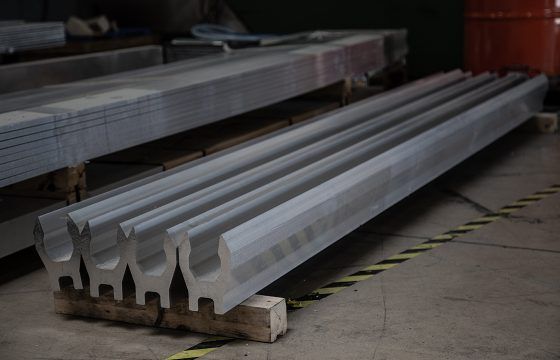
The cross-section of the EBOXX down tube is a 7000 series aluminium multi-chamber profile. The large chamber of the profile is milled and holds the BOSCH Powertube battery, the cables of the bike are routed through the small hollow chambers. An E-MTB with a multi-chamber down tube is much more resistant to torsional loads compared to bikes where only a large hole for the battery is cut into a simple tube. This results in a more precise bike on the trail.
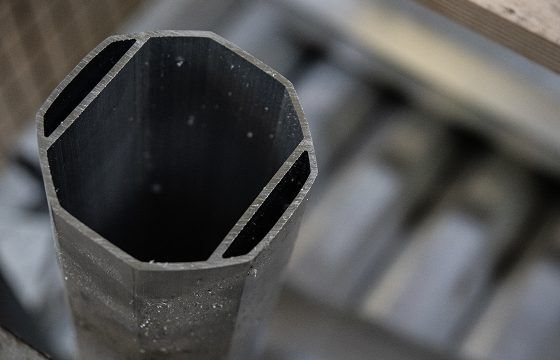
MACHINE HALL
At the machines, carefully selected materials meet the CNC programming. The material is loaded onto the machine automatically, the necessary tools are installed into the machine and the component is produced. When “running-in” the initial component is produced step by step by Bjarne Plate and Elias Neubauer. The tools are measured, the tolerances checked and accurate and repeatable production is ensured. After “running-in”, the component can be produced in large quantities on the machine. Various milling and turning machines are located in the production facility in Mehle. In addition to 3-, 4- and 5-axis CNC milling machines, there are also conventional lathes.
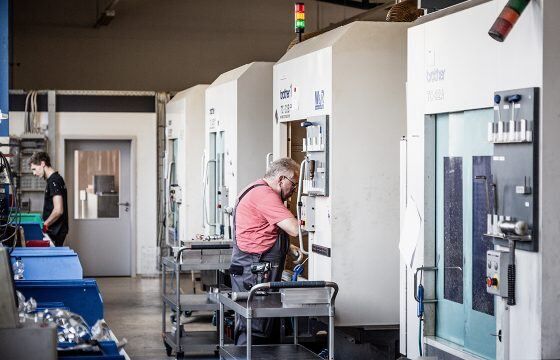
A HAAS milling centre is waiting for the next production batch. The use of a 5-axis milling centre does not make sense for every production step. It is often more economical to produce components on cheaper 3- or 4-axis machines.
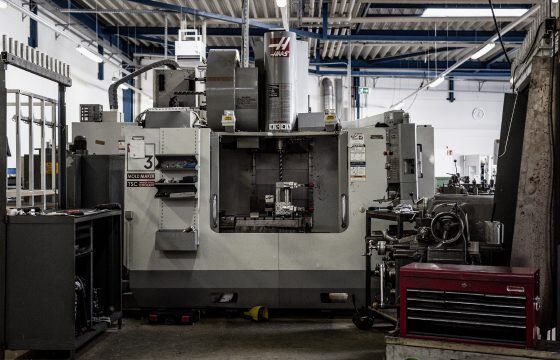
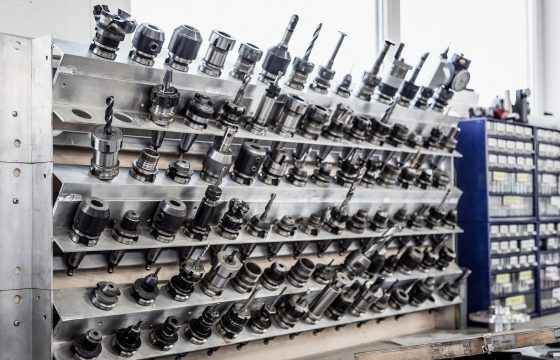
MILLED PARTS
MOTOR MOUNT
The central component of the new G1-EBOXX frame is the newly designed motor mount. This component is manufactured on a BROTHER 4-axis milling centre in 4 steps.
In the first step, the upper side of the raw material is face milled and mounting holes are drilled for the next setup. This step is necessary in order to mount the raw part optimally in the fixture for the following steps.
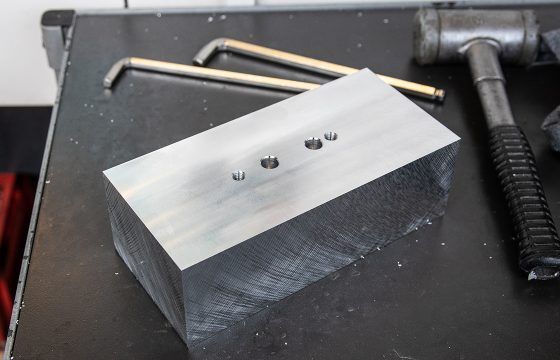
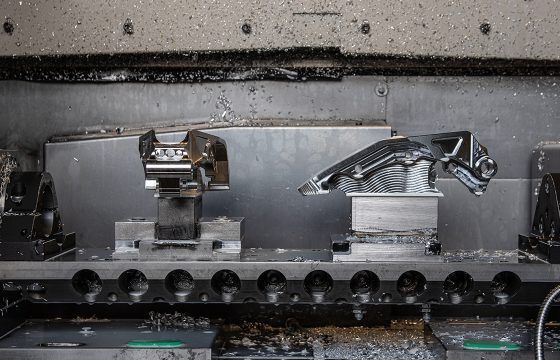
The component is completed in the 4th setup. The fluid cools the tools and flushes the chips out of the contact zone between tool and workpiece. All chips are melted down into new aluminium blocks.
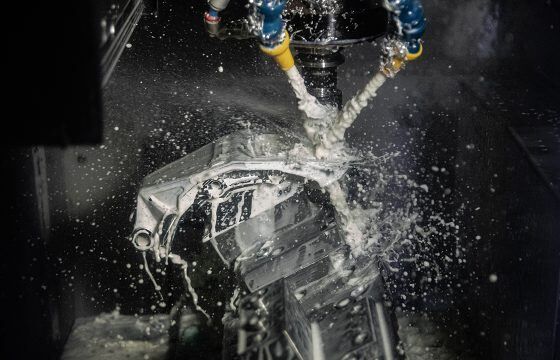
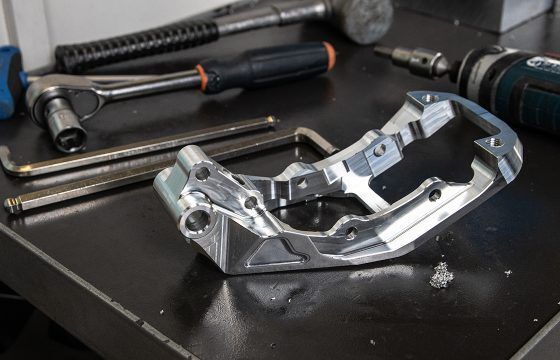
TUBE CUTTING
After all the milled parts have been produced, Daniel Trantow can begin cutting the frame to size. For each frame, a frame jig is first produced, which represents the geometry of the CAD drawing. In the initial steps, the tubes are cut by hand or by CNC machine and integrated into the jig. The frame is tacked and then removed from the jig. During tacking, the tubes are joined together by small weld seams.
Tube cutting starts with a drawing from the CAD system and a lasered template that transfers the geometry to the frame jig. It takes a lot of experience to estimate the welding distortion of the frame in advance and to adjust the jig accordingly.
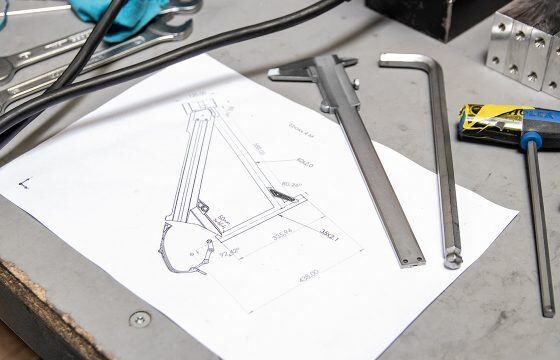
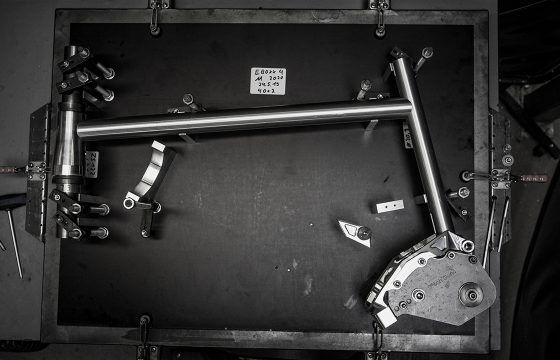
The clamped head tube in the frame gauge. No mistake should be made here. Every dimension must be correct. After tacking there is no possibility to change the geometry…
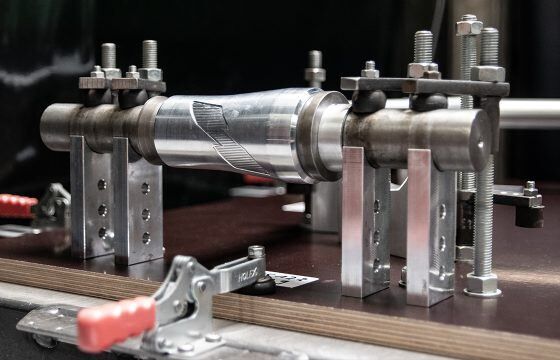
WELDING
NICOLAI frames have their own unique look. In addition to the puristic and timeless frame shape with straight tubes and fine milled parts, a NICOLAI frame can be recognised directly at the weld. NICOLAI seams are welded very flat to achieve optimum force flow between the components and minimize notch effects.
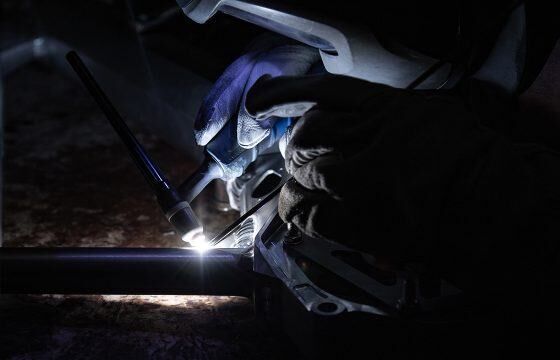
A G1-EBOXX main frame on the table of welder Sascha. A steel motor dummy is screwed in to minimise welding distortion due to heat input at the motor mount.
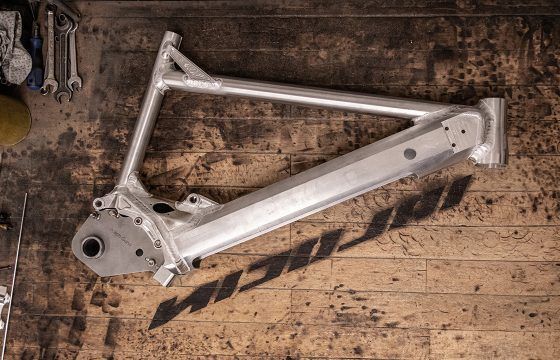
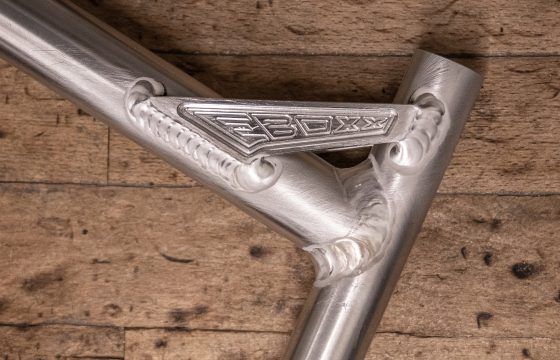
After the welding process, the frames are finally straightened and then heat treated in the furnace. After this ‘aging’, the frame has reached its optimum strength.
POWDER COATING PREPARATION
After welding and artificial aging, the frame is prepared for coating by Stephan Wickenhäuser and Martin Krause. NICOLAI offers three different finishes. In addition to powder coating (in any colour you can dream of!) and anodizing, the frames can also be supplied FACTORY RAW, the raw finish shows off the true beauty of our craftmanship and proves we have nothing to hide! The G1-EBOXX frames are offered in black powder coating as standard. For the colour of the powder coating to adhere, the frames must be grease-free and dry.
A G1-EBOXX main frame is washed by Daniel Jahn. Here manual work is in demand. This is the only way to ensure that the frames are free of grease and dust.
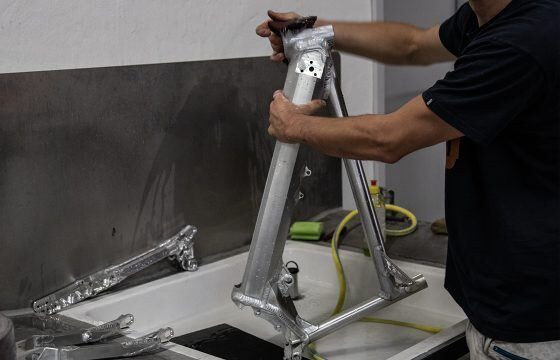
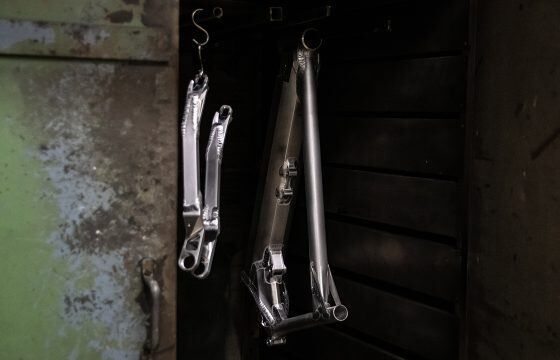
POWDER COATING
During powder coating, positively charged plastic powder is distributed over negatively charged components using a powder gun and then melted and cured in a furnace. The result is a robust and impact-resistant plastic coating. It is important that functional surfaces such as bearing seats or threads are kept free of plastic powder. This is achieved with 3D printed components that are inserted into the bearing seats.
A G1-EBOXX main frame before coating. The frame hangs on an electrode and is then sprayed dry with positively charged paint particles.
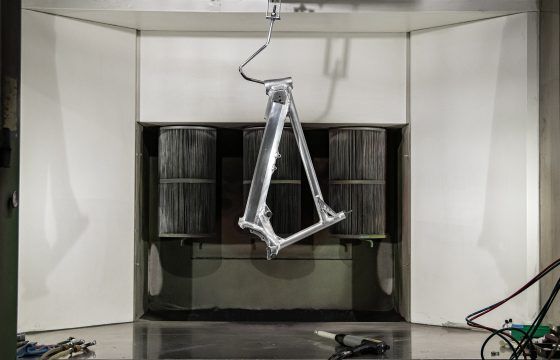
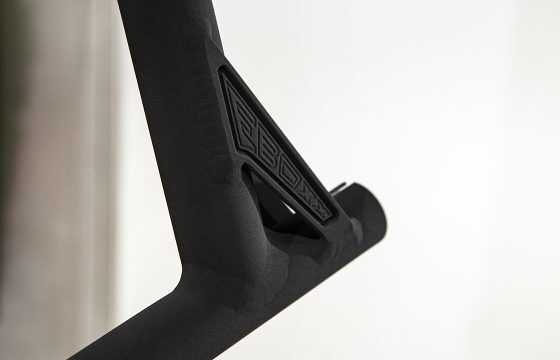
The seatstays are also coated. This picture shows the powder gun that distributes the black powder over the component.
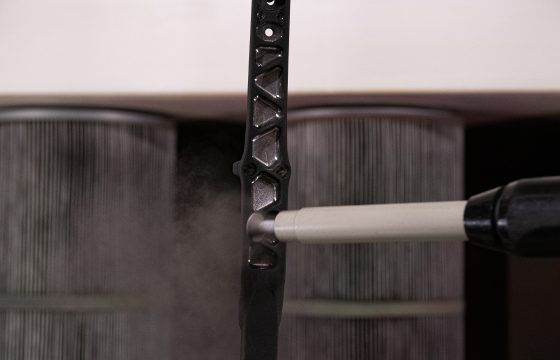
ASSMEBLY
At the end of the production process, the frame and the complete bikes are assembled. During assembly all production steps flow together. Claus Papendorf and Jens Kienlin fit the coated main frame, the swingarm and the compression struts with cartridge bearings and complete them with the coloured anodised finishing kits. Since every NICOLAI frame or complete bike is manufactured to customer specifications, it is important to document the special requirements and the equipment variations. The production step is completed with the optical and technical inspection of the frame and the final acceptance by a second man (the “four-eyes” principle).
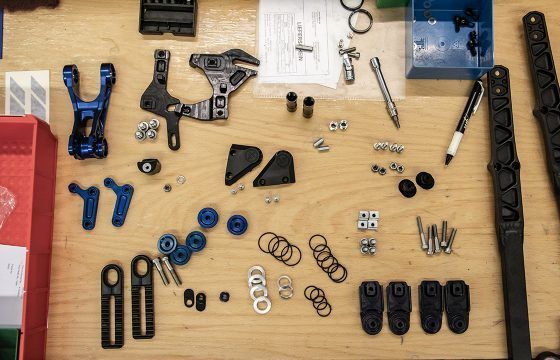
In model year 2020, the standard color for the G1-EBOXX is a black main frame with blue attachments. The bike can also be supplied in a different colour on request.
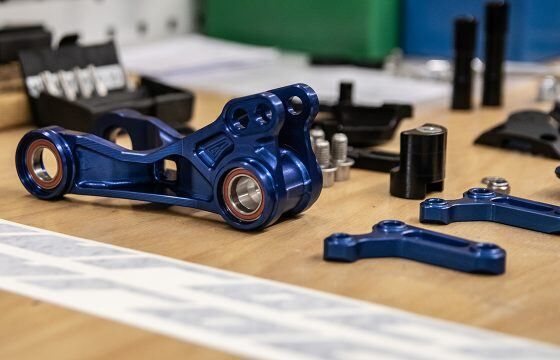
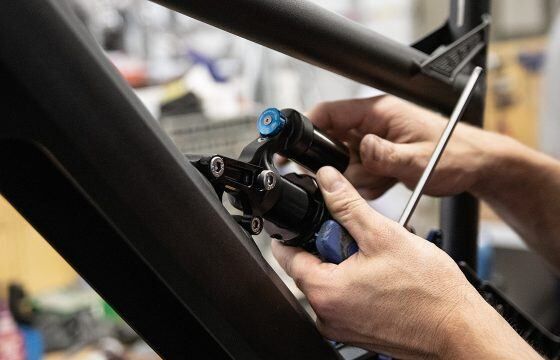
An assembled G1-EBOXX E14 frame is waiting for the complete wheel assembly.

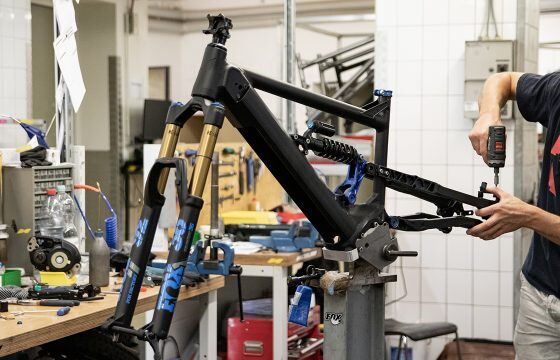
The complete bike is mounted by Daniel Jahn. Many components can be individualized on the complete bike according to the customer’s wishes. Wheel size, handlebar height, handlebar width, stem length, saddle width, grip diameter etc.
IT'S DONE
The G1-EBOXX 2020 with BOSCH Gen 4 motor. NICOLAI didn’t just take a BOSCH CX engine off the rack and screw it into a frame, but operated real product integration. The motor is protected from damage from below by an aluminium forged part. At the side and front, the motor is protected by its own rubberized parts so that air can still circulate. This newly developed air guide on the new NICOLAI G1-EBOXX ensures that the engine works quietly and does not get too hot on long climbs. The new system also scores on the battery side with 25% more range. This 625Wh BOSCH Powertube battery can be snapped into the NICOLAI G1-EBOXX from below. The completely redesigned frame has a modular design and can be fitted with 27.5″ or 29″ wheels. The adjustment is done by the headset and different screw-in elements, which we call mutators. The round tubes made of high-strength 7020 aluminium underline the classic NICOLAI look.
As this tour shows, the NICOLAI G1-EBOXX is not a standard E-MTB from Asian mass production, but an elegant high-end product tailored to customer requirements. With a maximum payload of 150 kg and 5 frame heights, every customer will be able to find a NICOLAI bike to suit their needs. You are welcome to visit us at our location in Mehle, take a test ride and get your own impression of the production. Contact us so that we can find a suitable date.